Implementing ON!Track with Laing O'Rourke
Laing O'Rourke tell us how they're using ON!Track asset management software across different projects
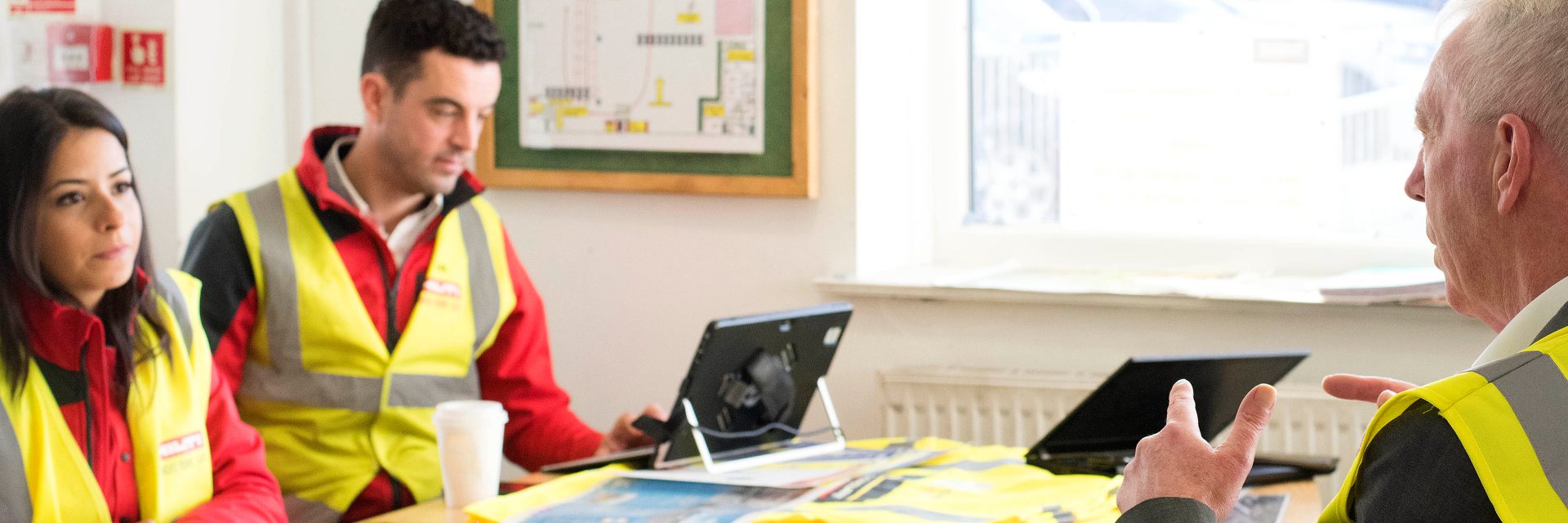
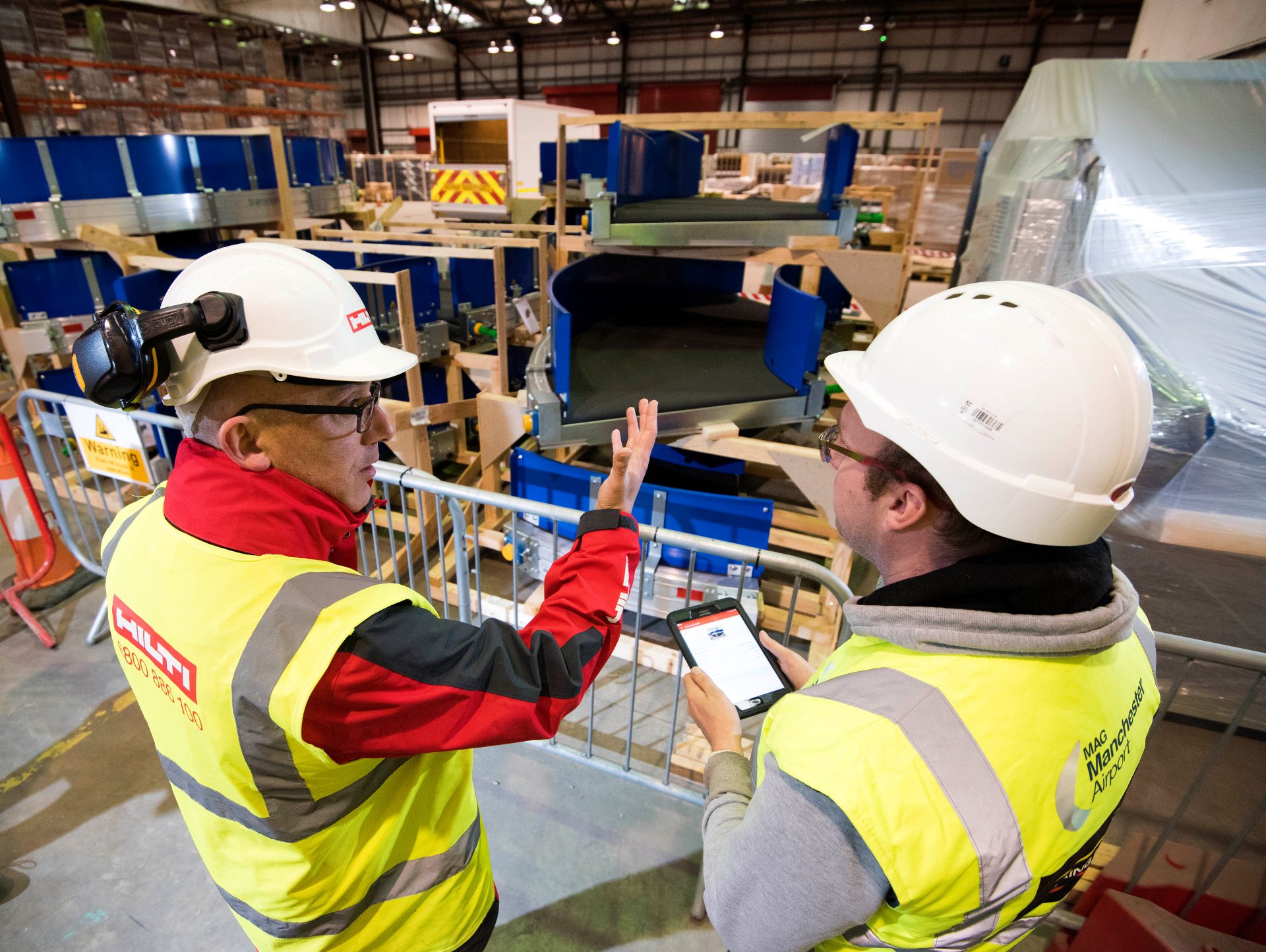
Laing O’Rourke was awarded the contract on the Manchester Airport Transformation Programme. Since 2016, they have carried out construction and design works on an extension of the existing Terminal 2 building to create Manchester’s “super-terminal”. Along with the six-storey Terminal 2 extension this includes, three new piers (one with a link bridge), a 3,800-bay multi-storey car park, ramp style forecourt and extension to the baggage hall.
We had the opportunity last month to meet with Mr. Ged McColgan, Logistics Manager at Laing O’Rourke about the implementation of ON!Track and how they plan to use it in the future across their different projects and sites.
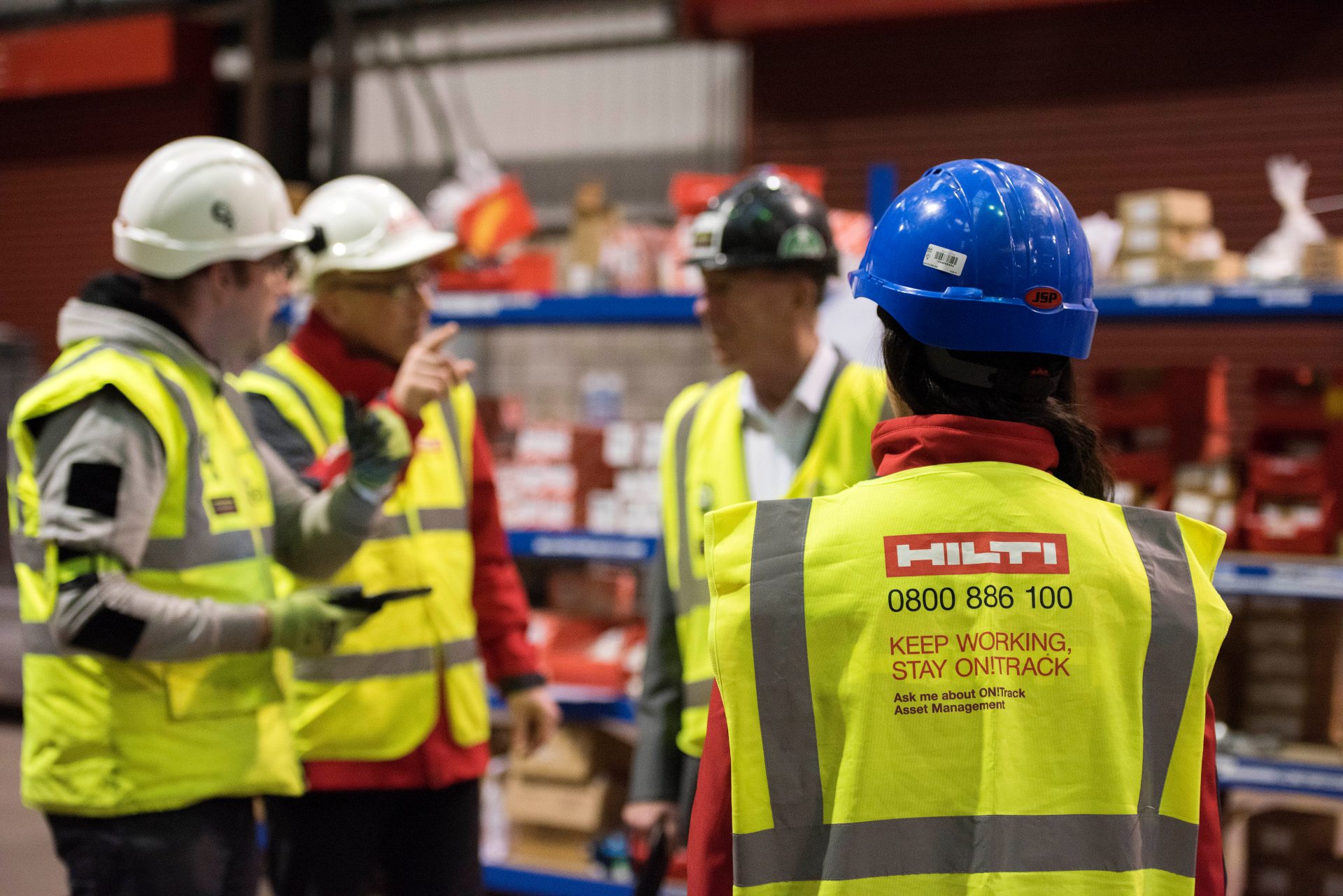
What do you like the most about the support Hilti offers?
Ged McColgan: The support we’ve received so far is good and most importantly: you answer the phone.
How would you see ON!Track benefiting you in the future?
Ged McColgan: The more you use ON!Track, the more you can realise what it can do. It certainly gives ownership of products and assets and full transparency.
Stocktaking is a win-win for me. The simple fact that you can go into a live environment where people are actually working and do a stocktake without interrupting their day is a bonus.
As we move on to other projects, the next step would be to take the learnings from this site and the most important thing: asset management.
Share